
Source: Supplied.
Coates’ internal basement retention solution provides an alternative to fabricated steel shoring, with two new hydraulic shoring products offering unbeatable load capacity and greater flexibility.
With surging timber and steel costs, energy price hikes and ongoing labour shortages, the Australian construction industry has been under significant pressure in recent years, as witnessed by a growing number of firms going bust.
Building contractors need to manage material costs, yet for large developments featuring multi-level basements, consulting engineers often specify a bespoke structural steel shoring system to support the excavation. This means the cost and availability of structural steel can have a huge impact on both construction schedules and budgets.
Alternatively, tie-back soil anchor solutions can be used, but these are often hampered by the proximity of in-ground structures and services such as sewer lines or gas mains, and the need to gain permission from neighbouring landowners to install ground anchors on their properties.
An alternative to structural steel
Coates, Australia’s leading equipment hire and solutions provider, offers building contractors an alternative to structural steel to shore large excavations. Customers can instead hire an off-the-shelf, internal shoring solution featuring proprietary, modular hydraulic struts and waler beams.
These products can be used again and again unlike single-use structural steel systems. This supports the industry in improving the sustainability of projects and helps customers like Stevens Constructions keep their basement build on track and on budget.
In 2022, the firm enlisted Coates to provide a full hydraulic shoring solution to support the excavation and construction of a four-level basement in Sydney’s Blacktown.
“On top of the delays that we would have experienced waiting for steel, there was just no buy-back value in a fabricated steel shoring approach for this project,” says John Russell, Project Manager for Stevens Construction. “The beauty of the Coates solution is that it is available, customisable and it can be reused.”
New industry-leading products: MP375 & HW500
Adding to its existing hydraulic shoring range, the company has launched two new hydraulic shoring and bracing products, the MP375 strut and the HW500 waler.
What makes these products so attractive for building contractors is their industry-leading load capacity and versatility. Both combine the compressive strength of steel with the ease of hydraulic actuation for length adjustment and pre-loading.
The super heavy-duty MP375 offers a level of support in basement-type excavations that exceeds the capacity of all other hydraulic struts currently available in Australia, says David Dragicevich, National Technical Engineering Manager at Coates.
“With a maximum safe working compression capacity of 375 tonnes, the MP375 allows us to design and implement even more efficient and cost-effective temporary works solutions, with the assurance and ease of using components that have been tested and proven in real-world construction applications,” David explains.
The HW500 waler, meanwhile, is where industry meets academia. Created in collaboration with Monash University and Van Der Meer Consulting Engineers, it features twice the capacity of the current industry-leading proprietary waler system, Coates’ own Mega Brace.
The HW500 system delivers the best of both worlds with flexibility and scalability. “This system can be used with sheet piling or concrete piled walls to create a standalone perimeter beam bracing solution,” says David. “It can also be supported by hydraulic strutting when there is a significant structural load or when support for particularly large excavations is required.”
Real-world benefits for the industry
What benefits do these innovative shoring products deliver for the construction industry?
- Flexibility: the MP375 can support high structural loads with fewer parts, providing extra space on site.
- Easy to scale: the MP375 can be coupled with tubular extensions for maximum load and spanning versatility.
- Faster and safer installation: there’s no need for welding or special tooling when installing these products, saving on time and complexity.
- Predictable systems: it’s harder to detect issues with fabricated steel until it’s too late, making it more unpredictable than pre-engineered components.
Want to learn more about Coates’ new hydraulic shoring products? Visit Coates or call 13 15 52.
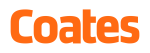
Coates, part of Seven Group Holdings (ASX: SVW), is Australia’s leading equipment hire and solutions provider, operating across a range of markets including engineering, mining and resources, infrastructure, manufacturing, construction, agriculture and major events. For more information, visit coates.com.au
COMMENTS
Reader comments have been turned off on this post.