
Source: supplied.
An Adelaide engineering company has further plans to tackle the global market with an export-friendly line of smart furniture and modular buildings.
Since the COVID-19 lockdown, Specialised Solutions has seen strong demand for its line of off-grid park benches and shelters and its modular buildings.
Worker and supply shortages in the building and construction industry and councils zeroing in on renewable energy projects are behind the demand for its cutting-edge products.
Brad Riddle, the company’s national business development manager, said Specialised Solutions were now eyeing more opportunities on a global scale.
Riddle said the company has distributors in the United States and New Zealand but said there is “strong interest” from European and Middle Eastern markets.
“We are working on an export version of our products,” Riddle said.
“We’re still working on that, but it will be a little more transportable and more modular.
“A number of our products are larger and made of aluminum and steel and so we need to look at transport efficiencies to ensure that we can still be competitive in the international market.”
Growing demand
Based out of the Tonsley Innovation District in Adelaide, South Australia, the company has been manufacturing its Sedi line of smart furniture for the last three years.
The original outdoor bench has since spawned bins, bike racks and heaters harnessing their power from the sun.
Designed by JPE Design Studio, the furniture is made from steel and sustainable timber and, using a small battery, can provide Wi-FI, lighting and charging ports to people.
Riddle said the company saw increased demand for the unique products during the COVID-19 lockdowns.
“I think COVID-19 has put a new focus on public spaces and councils are looking for innovative ways to deliver in those spaces, and our products fit within that perfectly,” Riddle said.
“We’ve also seen large public infrastructure grants to councils come out in the last 18 months, 24 months with COVID-19, so we’ve had a renewed focus on those public spaces.”
Riddle said there has also been a growing appetite for modular buildings in regional areas struggling with housing issues.
“A lot of places can’t get builders, so people are looking at different systems and different processes for how they would traditionally do something, in particular regional areas.”
In May, the company installed three modular buildings, including a foreshore cafe, visitor’s information and a library in the South Australian town of Whyalla for the local council.
Riddle said the council couldn’t find local builders to complete the work in time.
The company constructed the modular buildings at the company’s base in the Tonsley Innovation District. They then shipped the buildings to the South Australian town to be installed on-site.
“We’ve found our products cross a gamut of needs and requirements at the moment which works well, but we’re always looking at how we can improve the modularity in the production of what we do to reduce cost for the end consumer,” Riddle said.
An innovation hub
The Tonsley Innovation District co-locates a variety of manufacturing capabilities, which allows engineering companies like Specialised Solutions to work with design companies, as well as fabrication and manufacturing companies, all in one location to bring an idea to market.
Renewal SA’s Tonsley project director, Vince Rigter, said Specialised Solutions demonstrates the importance and ongoing need for traditional manufacturing capabilities to deliver new highly technical advanced products.
“To bring high-end technologies to life you still need a “carrier”, which often is defined in a classic form of metal fabrication. These businesses are such an important part of the value chain to get a product from an idea on paper to a product that adds value to the community,” Rigter said.
“Co-locating a variety of manufacturing capabilities is a key element of Tonsley’s vision in order to deliver commercial success of businesses in the district and growing economic development for the state.”
Tonsley once housed a Mitsubishi car assembly plant but is now home to more than 2000 workers in critical industries, including clean tech and renewable energy, medical devices, mining and energy services and automation and simulation.
This article was first published by The Lead South Australia.
Handpicked for you

After lighting up South Australian stadiums, VALO is looking to take its business international
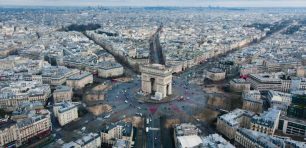
COMMENTS
SmartCompany is committed to hosting lively discussions. Help us keep the conversation useful, interesting and welcoming. We aim to publish comments quickly in the interest of promoting robust conversation, but we’re a small team and we deploy filters to protect against legal risk. Occasionally your comment may be held up while it is being reviewed, but we’re working as fast as we can to keep the conversation rolling.
The SmartCompany comment section is members-only content. Please subscribe to leave a comment.
The SmartCompany comment section is members-only content. Please login to leave a comment.