
The US Air Force's new Red Hawk jet trainer has the designation eT-7 to reflect its purely digital design and testing process. Source: Military Wiki.
The machines our world relies on were once designed with whatever tools designers had — sketches, plans, slide rulers, and sometimes, just good old-fashioned guesswork.
Often, it wasn’t until something was actually built that designers could see if it actually worked as they had intended.
Advances in technologies, such as modelling and computer-aided design, helped creators get closer to reality with their designs, but an extensive testing and redesign phase was required for prototypes to pick up any issues before production began.
This could be a lengthy process, holding up advances in technology or technique for years until flaws were ironed out.
But the United States Air Force and the aircraft manufacturer Boeing have just changed the game completely, designing and testing a new jet trainer aircraft to operational level using just computer modelling and simulation.
Known as the Red Hawk jet trainer, the new plane will have the designation eT-7 to reflect its purely digital design and testing process, which the Air Force said allowed the plane to proceed from “from computer screen to first flight” in three years.
The plane ‘flew’ thousands of simulated hours to test its performance, while its parts were even laid out and assembled digitally before a single piece of metal was cut in real life to test its design.
Physical testing once the plane was built merely confirmed what the computer had already shown.
The heights beyond digital transformation
This an enormous breakthrough in aerospace design, where it can take decades to design and test new planes. But it’s also a clarion call for the sheer power of the digital tools now available.
The all-digital design and testing process for the eT-7 came after the US Air Force and Boeing instituted a decades-long digital transformation process.
In the wider business world, there is a greater focus on the need to embrace digital transformation, how to successfully conduct such a process, and the importance of pursuing it.
But little coverage is given to the new horizons such a process opens up.
The power of digital transformation is more than simply bringing a business up to modern standards with technology and interfaces.
The power lies in what the process makes possible — empowering businesses to fundamentally change and improve everything they do, and scale heights of achievement and innovation hitherto unavailable to them in the analogue world.
But a major lesson from the development of the Red Hawk is that digital transformation didn’t just reset the playing field for aerospace design, it also empowered people at Boeing and within the US Air Force with tools to create something revolutionary.
This is the essence of what’s known as human-centred design.
More than simply designing with people in mind, human-centred design elevates the abilities of the people participating in its use. And digital transformation that includes humans in its calculations will always produce superior results.
Always start with the user
If a plane can be designed and tested in three years using digital tools, then there’s no end of possibilities for advanced technologies being used to speed development in other fields.
Crucially though, the eT-7 is a jet trainer — a machine that needs to be forgiving to the new human pilots who will get in its cockpit and allow ease of use and function.
The designers had to digitally recreate the physical conditions the pilots would experience, everything from how much leg room was available to the ergonomics of the controls.
This was done by empowering the designers with digital assets such as virtual reality headsets and AI-driven testing processes, ensuring the team had everything at their disposal to create the new design and make sure it was usable to its ultimate operator, a human pilot.
Taking this theme wider in the realm of digital transformation, it’s vital that any improvements that are made to an existing business digitally start with the user in mind.
The efficiencies and cost-savings that can arise from switching a paper filing system to a digitised record are enormous, but if the processes that govern the new way of working aren’t considerate of how people like to work, then it’s likely doomed to fail.
The best kinds of successful digital transformations always design human-friendly work processes, consider how the technology will actually be used in the field, and make these points their starting positions.
As impressive as the Red Hawk’s digital design is, the fact that it’s all focussed on training a human is even more important.
Use technological complexity to simplify human processes
There is always fear the technological advancements will replace humans, and this is felt especially in aerospace, as drones and other unmanned aircraft continue to develop.
But technological advancements have actually allowed human pilots to have finer control over flight performance, using the complexity of computers to minimise the effort it takes to fly the machine — something earlier pilots who relied on brute strength would appreciate.
New aerospace technology also allows greater insights in terms of spatial awareness, flight efficiency and in a military context battlefield awareness.
This is all achieved by using technology to remove complexity from human users and free them up to think, observe and take informed action — the true value of a human operator.
This is the ultimate point of digital transformation that emphasises human-centred design.
Faster, stronger, better with human-centred design
The digital transformations that led to the all-digital design and testing of the Red Hawk show how modern technology can combine advancements to remove complexity from a process, creating a new way of working that produces swift, efficient results.
But it also shows the importance of human-centred design, where the end product needs to be amenable to its human operators, and where the working processes need to be matched to the people governing them.
Bringing things full circle, that’s the true power of digital transformation, seen in aerospace projects such as the Red Hawk.
For years, people have had to design work processes and machines using inaccurate methods, hoping for the best outcome, then tweaking as they went to find the best solution.
But embracing digital means we can create the best possible workflows and develop highly advanced machines and processes before we hit the start button.
And if things are designed with the end-user in mind instead of just the purpose, then the probability of success becomes higher and higher.
So while it’s important to look at the benefits digital transformation will bring, it’s also worth looking up and seeing the heights that can be achieved.
And who knows, you might see a digitally-designed plane up there too.
Handpicked for you

French social media startup bags $65 million to fuel growth in the Aussie market
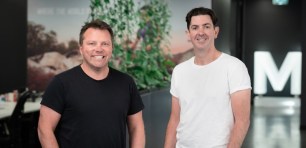
COMMENTS
SmartCompany is committed to hosting lively discussions. Help us keep the conversation useful, interesting and welcoming. We aim to publish comments quickly in the interest of promoting robust conversation, but we’re a small team and we deploy filters to protect against legal risk. Occasionally your comment may be held up while it is being reviewed, but we’re working as fast as we can to keep the conversation rolling.
The SmartCompany comment section is members-only content. Please subscribe to leave a comment.
The SmartCompany comment section is members-only content. Please login to leave a comment.